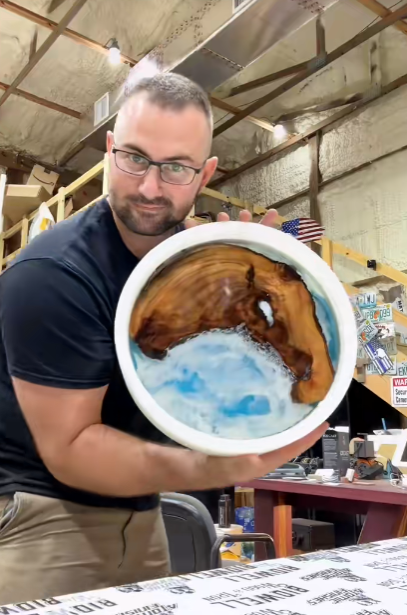
Drying lumber is one of the most critical steps in woodworking, lumber processing, and furniture making. If you’ve ever wondered why high-quality wood products can be so expensive or why woodworkers are so particular about their materials, it often comes down to moisture. And here’s a fact that might surprise you: on average, it takes one full year per inch of thickness to air dry lumber. That’s right—if you’ve got a 2-inch-thick slab of wood, it could take up to two full years just to dry properly using natural air-drying methods. But the story doesn’t end there. After this lengthy process, many lumberyards—including ours—use a Nyle Kiln to complete the drying process, ensuring stability and eliminating insects or larvae hidden deep inside the wood fibers.
Why Drying Lumber Is So Important
Wood is a hygroscopic material. That means it absorbs and releases moisture depending on its environment. When freshly cut, lumber can contain anywhere from 30% to 200% moisture content, depending on the tree species and time of year it was harvested. If you try to build furniture, cabinetry, or flooring with green (wet) wood, it’s a disaster waiting to happen. It will warp, crack, split, or twist as it dries, ruining whatever you’ve built.
To prevent that, lumber needs to be dried until it reaches what’s called equilibrium moisture content (EMC)—usually between 6% and 12%, depending on the climate where the wood will be used.
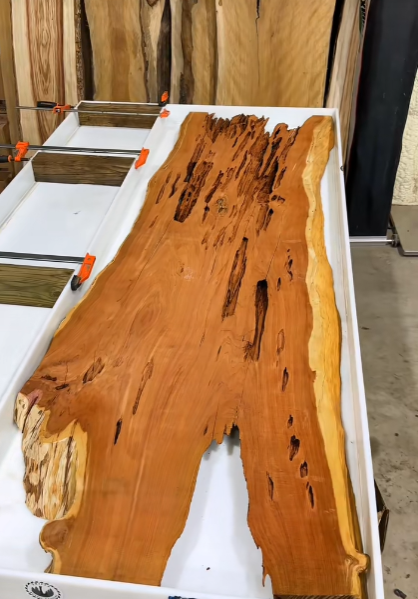
The Air-Drying Process: One Inch Per Year
Air drying is the most traditional and natural method of reducing the moisture content in wood. After cutting the logs into slabs or boards, the lumber is stacked with spacers (stickers) in between each board to allow airflow on all sides. These stacks are typically kept under a roof or a shed with good ventilation but protected from rain and direct sunlight.
Here’s where the patience comes in. As the rule of thumb goes, it takes one year to air dry each inch of thickness. So a one-inch-thick board may be ready in 12 months, but a 3-inch slab could take 36 months or more.
There are a few things that can influence the drying time:
- Species of wood: Hardwoods like oak and walnut dry more slowly than softwoods like pine.
- Climate: Hotter and drier conditions may speed up drying, while humid or rainy environments can delay it.
- Airflow and stacking method: Proper sticker spacing, elevation, and ventilation significantly affect how evenly and quickly the wood dries.
Despite its long duration, air drying is gentle on the wood, reducing the chances of internal stress, surface checking, and other defects. However, air drying alone is often not enough, especially if the wood is destined for indoor use or fine woodworking.
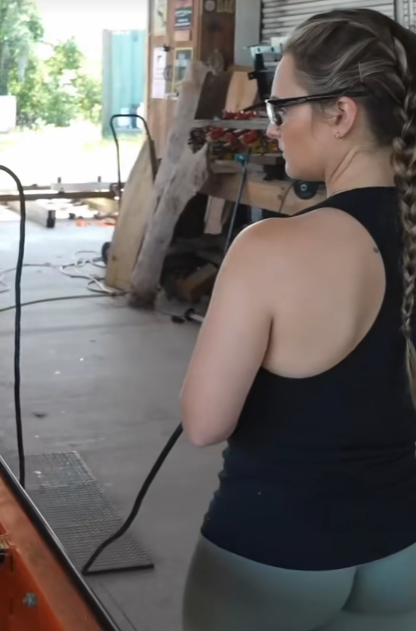
Why We Use a Nyle Kiln After Air Drying
After our lumber has been patiently air dried for months—or even years—we move it into our Nyle Kiln system. This step brings the wood down to a final, usable moisture content, usually around 6-8%, perfect for furniture and cabinetry. But the kiln does more than just dry—it sterilizes the wood as well.
A Nyle Kiln is a type of dehumidification kiln that uses controlled heat and humidity to dry wood faster than air drying, but without causing damage. It allows us to:
- Precisely control the drying process to avoid warping or case-hardening.
- Kill bugs, larvae, and mold spores that might have survived air drying.
- Speed up the final drying while still preserving the quality and character of the wood.
While traditional kilns can be energy-intensive and risky if used improperly, the Nyle Kiln is known for being efficient, environmentally friendly, and ideal for small to mid-sized lumber operations like ours.
The Importance of Bug and Mold Prevention
If you’ve ever used reclaimed wood or improperly dried lumber, you might have noticed signs of insect damage—tiny holes, powdery dust, or even live bugs crawling out. That’s because certain pests like powderpost beetles or termites can live deep within the wood, and air drying alone doesn’t always kill them.
By putting our lumber through the Nyle Kiln after air drying, we raise the internal temperature high enough to kill off all insect eggs and larvae. This process not only protects the integrity of the wood but also ensures it’s safe for indoor use, especially in homes and commercial spaces.
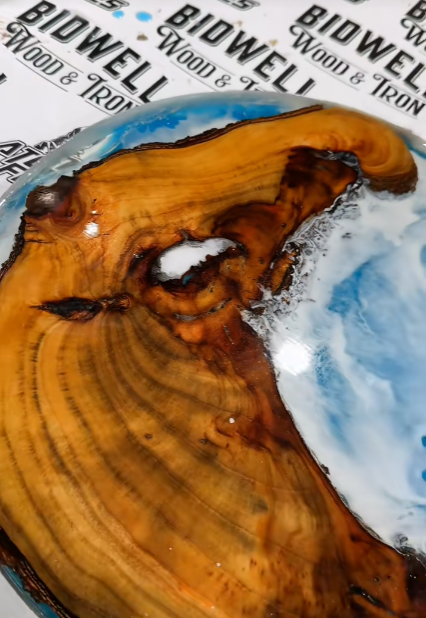
Balancing Tradition and Technology
Our drying method—starting with slow air drying, followed by controlled kiln drying—represents the best of both worlds. It honors the time-tested tradition of patient, natural seasoning while embracing the precision and reliability of modern kiln technology.
Many large-scale lumber operations skip air drying entirely to save time, going straight to high-heat kilns. While this can work, it often stresses the wood, leading to cracks, honeycombing, or other internal damage. We prefer to let nature do its job first, then refine and finish the process in the kiln. This results in higher-quality, more stable, and longer-lasting lumber.
What This Means for Our Customers
Whether you’re a DIY builder, professional woodworker, or just someone looking for a beautiful live-edge slab for your dining table, the drying process matters. Well-dried wood is:
- Easier to work with using hand tools or machines
- Less likely to shift or warp after your project is built
- More resistant to insects and decay
- Safer for indoor environments
We’re proud to offer lumber that has gone through such a thorough and careful drying process. It’s not just about selling wood—it’s about offering a material that’s ready for your creativity, your tools, and your trust.
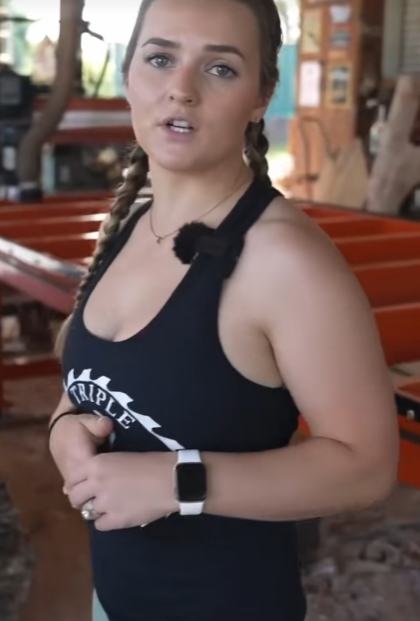
Final Thoughts
Drying lumber isn’t a quick or easy process, but it’s absolutely essential to producing wood that’s usable, reliable, and beautiful. The fact that it takes one year per inch to air dry lumber really puts into perspective the value of well-prepared wood. It’s a waiting game, but one that ensures your projects won’t be ruined by warping, splitting, or pests.
At the end of that journey, our Nyle Kiln gives the lumber its final polish—a stable, bug-free, and moisture-balanced finish. So the next time you admire a perfectly flat, smooth, knot-free piece of hardwood, remember: behind every great board is years of patience, craftsmanship, and care.